In spring, Uttar Pradesh in northern India reveals a flat landscape scattered with emerald green plots of wheat. Acid yellow flowers from mustard seed punctuate the horizon as women in hot pink sarees tend their crops. As one of India’s largest states – over 200 million people live here – it’s an extraordinary sight, vibrant with activity. This rural landscape is home to the best rug weavers in India and everyone here is engaged in some way or another with the very detailed and complex business of making rugs.

This specific region of Mirzapur and Bhadohi is the hub of production and dates back to the 16th century during the reign of the Mughal emperor, Akbar. Rug weaving has particularly flourished here since the late 1880s and everything is done by hand on a staggering scale. Small workshops are tucked away across cities, towns and rural hamlets. One hundred per cent of what’s produced is exported across the world and the craftsmanship can be exceptionally high. Provenance is so important to Western consumers and an increased transparency surrounding how these products are made is essential. There is still a surprising assumption in the UK that conditions are generally poor and weavers are badly paid – or worse still, that children are part of the workforce. In reality it’s the opposite; large airy factory spaces flooded with bright, natural light filtering through tall windows can host a team of highly skilled craftsmen working carefully at their tasks.
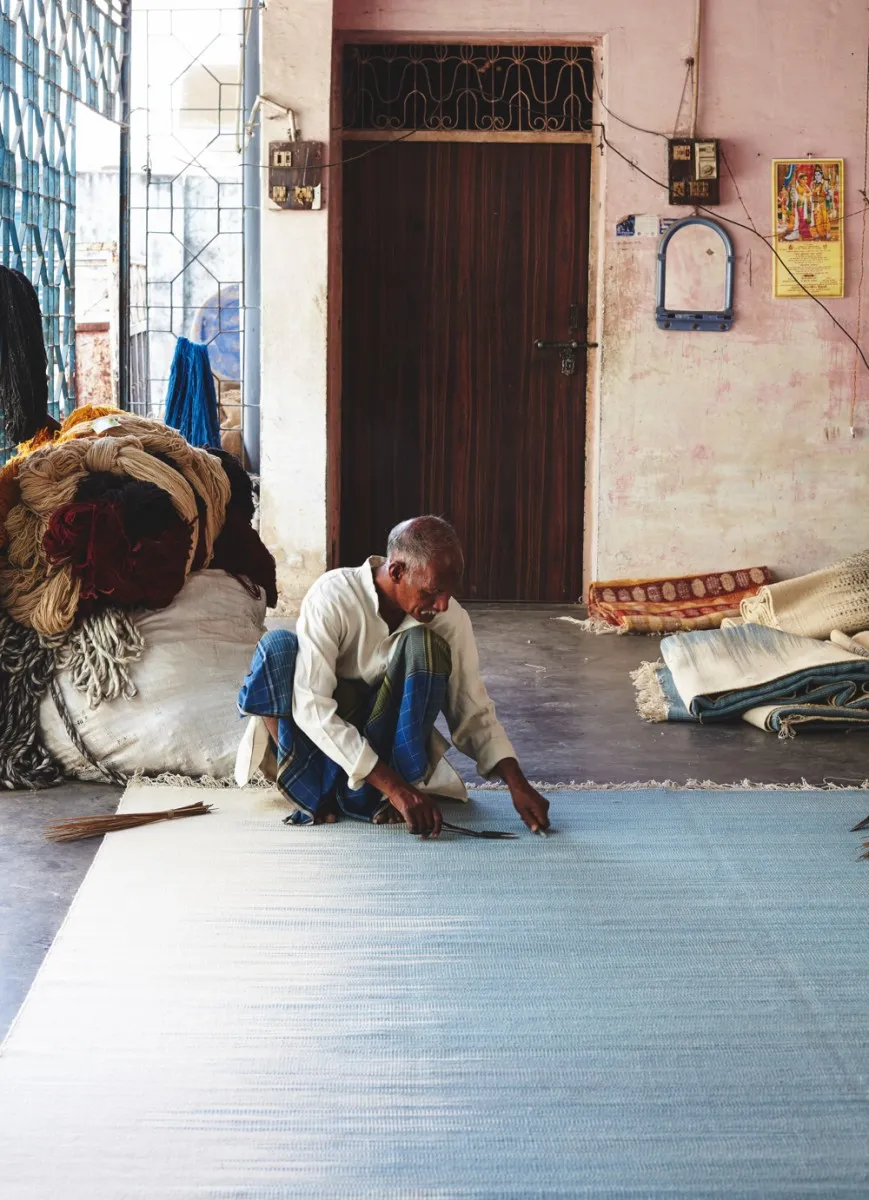
In praise of flat weave
Historically the flat weave is seen as the lesser cousin to the more luxurious pile carpet, which is hand knotted. Pile carpet can be produced on a vertical loom or it can be gun tufted by shooting wool through a base cloth to create a surface of wool ends that are then trimmed to a close pile. Softer underfoot and more expensive to make, a pile rug has always held an elevated status. However, real beauty can be found in the flat weave. Perfect on wooden or stone floors, often double-sided and, in many ways, more suited to modern interiors (and certainly better in hotter climates), there are many positive attributes to recommend the flat weave

The extraordinary thing about rug weaving is the number of processes that must occur in a specific sequence. To begin, the weft (the horizontal threads) of natural wool must be wound into hanks for dyeing. Whirling drums catch the light as they spin the wool. There are few sheep in India and the quality of their wool is not good, so almost all of the wool used is from New Zealand or Sardinia, shipped to India in vast quantities. The warp (the vertical threads) are a robust cotton and remain undyed. These are wound into ‘warps’ on a large frame and will create the backbone of the rug – no warp threads will be visible in the final piece.

Gelim or kilim?
There are several different types of weaving technique and loom. A horizontal peddle loom (often built into the floor) is operated by one, two or three weavers depending on the width of the final rug and creates a linear patterned or striped flat weave. The weavers work in tandem with impressive precision, energetically throwing a wooden shuttle loaded with dyed wool across the warp threads. ‘Gelim’ rugs originate in northern Iran and use a specific dip-dyed weft technique that creates a feathered ikat blur of dynamic colour. ‘Kilim’ refers to another ancient technique that originated throughout East Asia. These are woven on vertical looms like a tapestry. The motif is usually staggered, geometric and rather complex. Most will recognise this technique as it is readily available in many of the UK’s high street stores.

The final technique of rug weaving, which is less common, is made with a Jacquard loom. Housed in vast sheds, their atmospheres loud with movement, these huge, 100-year-old looms are strung with myriad threads. They enable more complex weave structures to be achieved through their many shafts and programmable punch cards. These machines are the precursor to our modern computers and are awe-inspiring to see in action. Once the rugs are complete, they are cut off the looms, trimmed, edges bound, washed, stretched and finished carefully by hand, ensuring there are no faults. A man crouching in a yoga pose trims loose threads and sweeps them away giving the rug a final close look. Its surface is flawless.

This particular rug producer is highly dedicated to his business and his weavers, and as they gather in their workshops overlooking the central garden of the factory there seems a real sense of pride among them. He explains that once they join his 4,500 strong workforce they tend to stay for life. A process of improvement and innovation is happening here: a constant search for better techniques, end products and craftsmanship. An unexpected integrity lies within these walls. The rug weaving future is looking bright here; much like the dye workshop rooftop, where an explosion of jewel-like colours dry in the fading afternoon sun.

The full feature on Indian rug weaving by Ptolemy Mann appeared in the Summer issue of Homes and Antiques.
Photographs: Katya De Grunwald