The rarity of antique printed fabrics in a length and condition to hang as curtains or cover a sofa has made machine-printed designs copied from period textiles the main option for filling the void. Modern copies are all well and good, but what about block prints? Fabric hand printed from sets of original carved wood blocks with a known date may not offer the complete antique package, but as many blocks are more than 150 years old, this ups the provenance rating considerably.
What is wood block printing?
Wood block printing is the grown-up version of potato printing that children enjoy. A design is carved in reverse, colour is applied to it and the pattern is stamped onto paper or fabric. This technique, first found in ancient civilisations in China, Egypt and India, took root in England in the 17th century, when printed and painted textiles from India became more widely available.
English block printing reached a high point in the 18th century and continued through the 19th, with William Morris hand block printing his designs using natural dyes. Although gradually overtaken by machine printing, block printing for designs of high esteem carried on into the early 20th century.
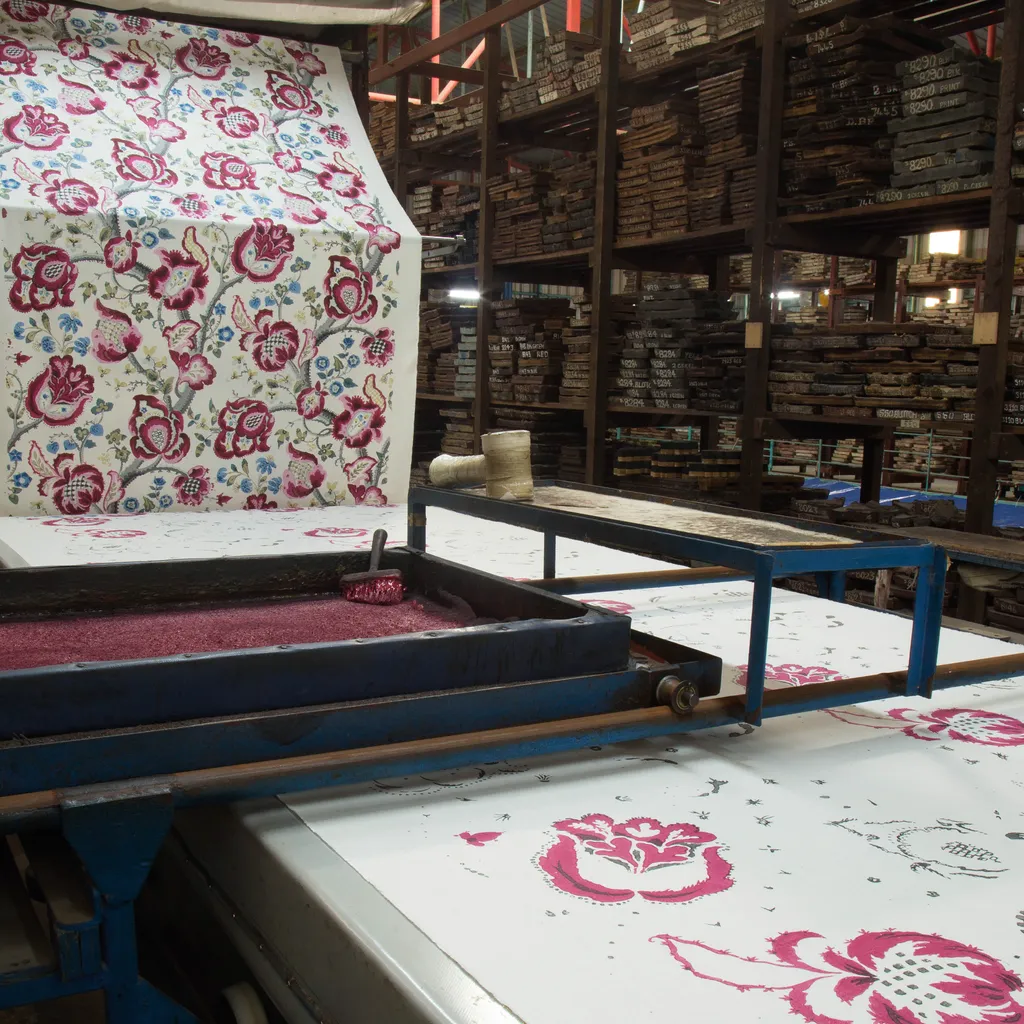
Block prints are in the spotlight again at the moment, with several fabric companies including them in their collections. Most are one-colour motifs cut into a single block and stamped onto cotton or linen. The work is still done by hand, usually in India.
Even at this basic level, block printing is exacting but there is a huge jump between printing a single motif and block printing intricate patterns with many colours from antique wood blocks. A dance sequence of multiple complex steps, or working up a difficult jigsaw puzzle, are useful comparisons.
Printing from antique wood blocks continues today largely thanks to the determination of Paul Turnbull of textile printers Turnbull Designs. He describes Turnbull as custodians of block printing and the last company with the skills necessary to produce these complex historical patterns.
The company has been in continuous production since 1881, and for the last 20 years it has been printing from its specialist unit in Thailand, where the historical blocks are repaired and blocks are cut for new designs. Leading fabric houses that commission Turnbull to block print designs for their collections on linen and cotton include Jean Monro, Hazelton House, Ralph Lauren, Lee Jofa and Schumacher, among others, all either based or represented in the UK.
How are printing blocks made?
Blocks are made from layers of hardwood, often sycamore, each put together in sections with the grain going in different directions, then backed with a softwood layer and glued together under pressure to prevent warping.
Each block is about four inches deep; smaller ones fit the printer’s hand and larger blocks have hand-holds cut to help them be positioned accurately on the fabric using special copper registration pins. One block is required for each element in the design and for each colour, so a complex design can require more than 250 blocks and 15 colours for each pattern repeat.

How are the designs created?
The design for each block is drawn on its smooth face and wood is cut away from areas surrounding the main design element. Fine details that cannot be carved accurately are created from strips of copper embedded in the wood. Larger areas of colour are applied by using sections of felt inlaid into the block, which act like an ink pad.
Colour is put onto the blocks by means of a felt cloth, which is known as a sieve. During a seven-year apprenticeship, printers learn how to position and apply ink to each block. Each layer of colour is allowed to dry before being overprinted by a different colour, called the fall-on.
‘The layering of colours, coupled with the handcrafted vagaries, help to provide a unique character and depth,’ says Paul Turnbull. ‘The reason people love block-printed textiles is the way the application of each block by hand gives subtle differences in pressure and positioning. This creates a unique, one-off print mark. Block-printed textiles represent the pinnacle of handcrafted textile printing.’
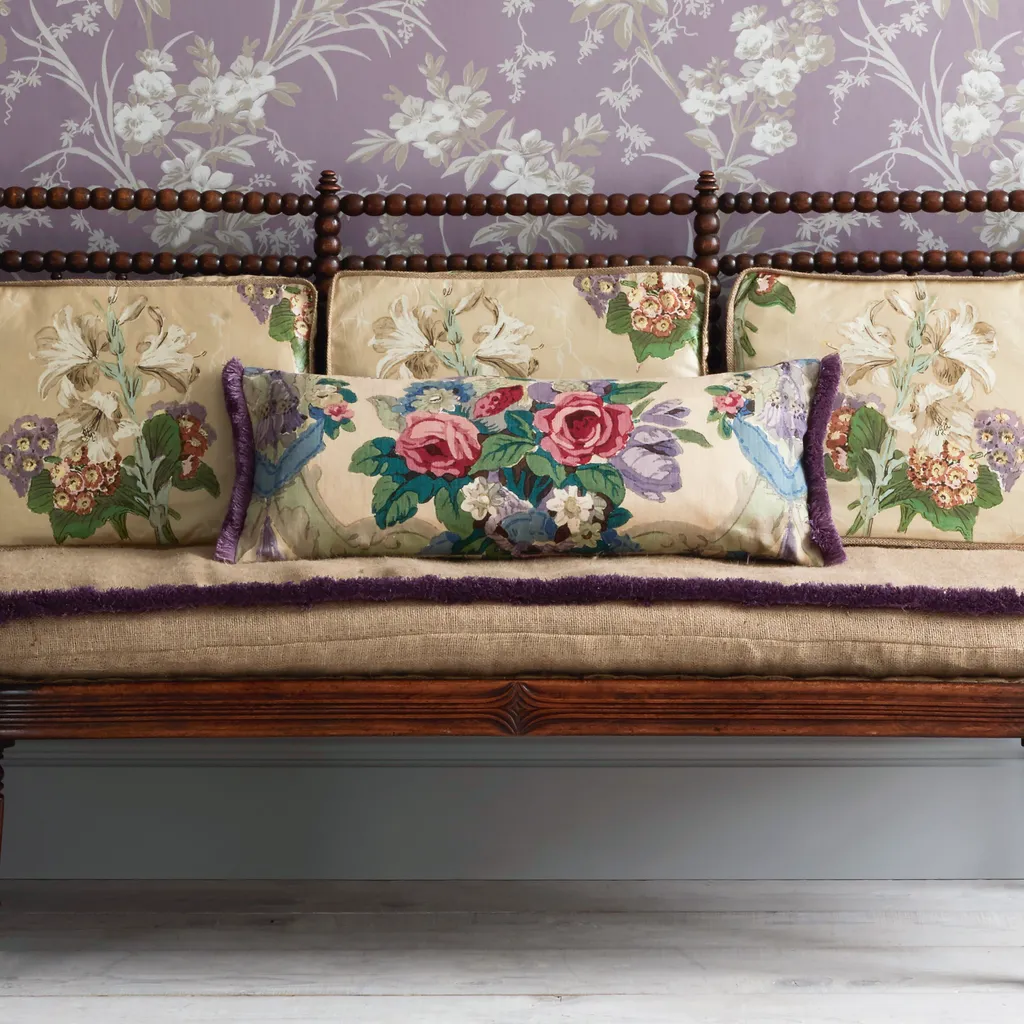